Robotics in NDE
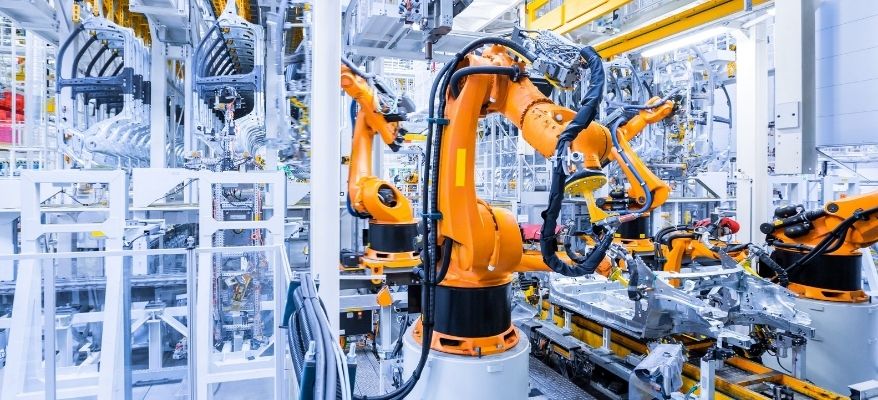
The research team at the Centre for Ultrasonic Engineering (CUE) at the University of Strathclyde has been researching the use of robotics in NDE since 2006. Early work on small mobile robot platforms for delivering ultrasonic and magnetic flux leakage measurements was matured with NNL into an on-site inspection at Sellafield supporting Magnox reprocessing life extension in 2012. Subsequent work on mobile robotics concentrated on bringing classical robotic path planning and location systems (such as SLAM–simultaneous location and mapping) together with novel approaches using ultrasound to provide both NDE and path planning data.
Working with supply chain partners such as Eddyfi and the commercial Scorpion platform, the team has developed and licensed technology for improved robot path planning and ultrasonic data
capture. Strathclyde has worked with partners NNL and EDF on using unmanned aerial vehicles (UAVs) to capture vision data to perform accurate 3D surface reconstruction of assets, and to use
anomaly detection to identify surface defects on structures such as wind turbine blades.
Recent work with the Institute of Robotics and Intelligent Systems (ETH Zurich) has demonstrated contact based ultrasonic thickness measurement deployed from an overactuated UAV. In parallel with the mobile robotics work, since 2012 the team has investigated the use of industrial robotics for delivering in process NDE during manufacturing processes.
Early work funded through RCNDE demonstrated the proof of principle at low TRL, and then technology demonstrators with TWI and UK Manufacturing Catapult have matured the technology to TRL 5/6. June 2021 The Strathclyde team has supported TWI in developing the Intacom project supporting Rolls Royce and other key industry partners to use ultrasound to inspect complex geometry parts. At the Advanced Forming Research Centre in Glasgow, the team established a Flexible Robotic Inspection Cell used for aerospace component inspection for Spirit Aerosystems (a tier 1 supplier for Airbus). This technology is now being deployed in the new Aerospace Innovation Centre (AIC), operated by Spirit Aerosystems in preparation for transitioning into the production environment.
A current focus for the team is for in process NDE inspection of welded and additively manufactured metal components. Working closely with KUKA Robotics, Strathclyde have developed advanced in-loop robot path correction and control that allows for adaptive NDE processes to be realised, such that real-time path correction can be used as live NDE data is monitored. This allows sophisticated approaches to using NDE data to in form and control manufacturing processes (robotic welding and metal additive deposition) very much aligned with the new Industry 4.0 paradigm for manufacturing.
A recently completed IUK project “RoboWAAM,” has developed the world’s first commercial robot delivered wire arc additive manufacturing platform with integrated NDE capability (available in a standard shipping container through KUKA Robotics). Bringing together metallurgists and materials scientists through an EPSRC Program Grant (EP/R027218/1) has allowed the team to develop new methodologies for calibration and standardisation of defect detection in robotic welded and metal additive manufactured components and develop a range of robot deployed novel high temperature compatible ultrasonic wheel probes to utilise in these challenging manufacturing environments.
Looking to the future, a major new University investment at Strathclyde has created the Robotically Enabled Sensing Hub (RES). This facility will allow the team to collaborate closely with our
RCNDE partners to operate at scale on real industrial components (wing covers, pipe sections, large AM manufactured components) to demonstrate cutting edge NDE technologies including LIPA (laser induced phased array), eddy current inspection, Ultrasonic TFM imaging and defect visualisation thus developing the next generation of automated systems for NDE. Three themes of work have been identified for the hub: Physical Sensing (the NDE sensors themselves), Sensor Delivery Platforms (the robotics and automation), and Data Processing (interpreting and using the NDE data).
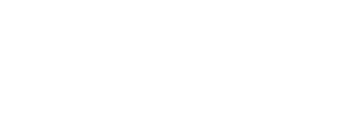
RCNDE – an internationally renowned membership-based industrial-academic collaboration that coordinates research into NDE technologies, ensuring research topics are relevant to the medium to longer-term needs of industry.