Detecting hidden corrosion on inaccessible areas of pipelines using EMATs
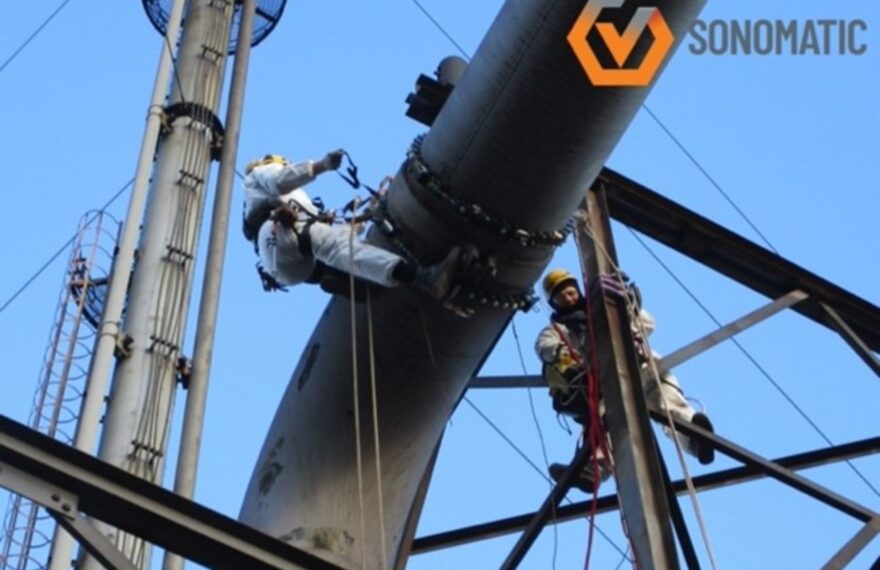
Pipework is a critical part of infrastructure in many different industries and requires regular ultrasonic inspection to ensure continued safe operation, checking the pipe’s structural integrity and avoiding degradation that could result in pipe leaks. One particular challenge for ultrasonic testing though is where it is not possible to directly access the surface region of the pipe where there may be hidden corrosion. This could occur between the pipe and a pipe support, where the pipe could be sitting on top of a pipe support or hanging from one. There are also cases where the pipe can be sitting on the seabed for example, where again direct access to the bottom surface of the pipe is not possible. Pipe corrosion can be external or internal, and often regular thickness gauging can be used to check pipe wall thickness, but the use of guided waves can cover a larger area in one measurement, saving time and costs.
The University of Warwick and Sonomatic Ltd worked on a EngD project to develop EMAT technology for the inspection of pipelines, especially focused on the detection and quantification of corrosion type defects on steel pipes under pipe supports. Sonomatic’s topside SH-EMAT inspection technique allows rapid screening of pipework and pipelines. The system is compact, battery powered and does not require couplant, making it extremely portable. Due to its design, the system can easily be deployed using rope access. The technique has been validated through blind trials and has proven its capability on-site at various locations around the world. Inspection under pipe supports is a major application for this technique, as it allows the condition of the material to be reliably assessed without the need for lifting the pipe from the support.
The outcome of the original R&D work through the EngD generated economic and environmental impact through improved infrastructure life expectancy, safety and structural integrity for Sonomatic and its clients. Over the past 8 years, the results of the EngD project has led to the creation of a significant number of new jobs and been used to add value to existing work scopes. The project transformed Sonomatic’s defect and leakage detection capabilities, ultimately protecting the environment – Sonomatic said “Locations that would not previously be possible to be included in an inspection campaign can now be inspected with relative ease…Degradation can be highlighted.. plans can be made for monitoring /repair before leakage or rupture of an asset occurs, minimising threat to the environment.” Cost savings too have been significant, with customers being delighted with that the service provided as ” … it gives them confidence in the condition of their assets without having to resort to more costly and time-consuming approaches.” Sonomatic operate their EMAT inspection systems in various locations around the world, both top-side and sub-sea and it continues to be an important area of the business for them and has delivered significant benefits and savings to their clients.
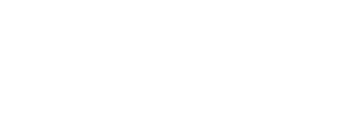
RCNDE – an internationally renowned membership-based industrial-academic collaboration that coordinates research into NDE technologies, ensuring research topics are relevant to the medium to longer-term needs of industry.